Индустрия 4.0 неизбежна. Как создать цифровое предприятие?
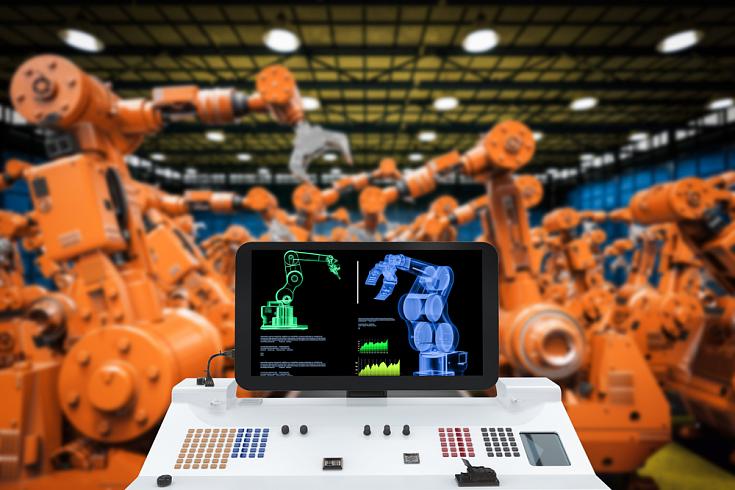
В последние годы промышленное производство по всему миру претерпевает значительные изменения. Распространение индустриального интернета вещей, «больших данных», роботизации и других технологий подталкивают нас к очередной промышленной революции – «Индустрии 4.0». С одной стороны, компании не всегда готовы вкладывать огромные средства в диджитализацию производства. С другой стороны, они сильно рискуют упустить возможность изменить ситуацию сейчас, пока промышленный интернет вещей находится на начальном этапе развития, и существует реальный шанс обогнать конкурентов на очередном повороте цифровой трансформации. В любом случае «Индустрия 4.0» – это уже не сказка, а реальность. По данным McKinsey Global Institute, для мировой экономики годовой эффект от внедрения интернета вещей к 2025 году может составить от 4 до 11 трлн долл. США, и значительная часть этой суммы будет обеспечена внедрением IoT в производство. Компании, которые смогут использовать все возможности цифровой революции, займут ведущие позиции на рынке.
Источник: http://www.tadviser.ru/images/c/c2/Digital-Russia-report.pdf
Что касается России, то она имеет ряд успешный кейсов по внедрению передовых технологий в производство, однако в целом по уровню диджитализации базовых отраслей промышленности страна значительно отстает от других стран. 90% оборудования на производстве в России не мониторится и не передает никакой информации о своей работе. При этом средняя загрузка станков в России колеблется от 30 до 50%, и мало кто располагает объективными данными, чтобы определить, почему самый главный показатель эффективности на производстве такой низкий, и как с этим бороться. По статистике Международной федерации робототехники плотность роботизации производства на российских предприятиях более чем в 20 раз ниже среднемирового показателя. На многих предприятиях страны не используются даже технологии прошлого поколения, такие как электронный документооборот или CAM-системы. Руководству таких производств не стоит отказываться от новых технологий из-за низкого уровня автоматизации, иначе с каждым годом их эффективность по сравнению с другими предприятиями будет только падать. Между тем, согласно исследованию McKinsey Global Institute, внедрение компонентов цифровой трансформации в российское производство к 2025 году ежегодно способно увеличивать объем ВВП страны на сумму от 1,3 до 4,1 трлн руб.
Цифровизация производства в соответствии с концепцией «Индустрия 4.0» включает в себя:
-
Компьютеризацию всего оборудования и рабочих мест сотрудников.
-
Подключение активов к интеллектуальным системам предприятия, которые управляют всем технологическим процессом (CAD, PDM, ERP, ЕАМ и другие).
-
Объединение систем, персонала, оборудования в единое информационное поле, которое позволит автоматизировать принятие простых решений и предоставит многоаспектные данные для предиктивной аналитики и создаст предпосылки для внедрения искусственного интеллекта. Одним из вариантов решения этой задачи является внедрение системы MDC (Machine Data Collection) в качестве фундамента цифрового предприятия для сбора всех производственных данных из разных источников в режиме реального времени.
Успешным примером такого подхода стала система мониторинга промышленного оборудования и персонала «Диспетчер» от российской компании «Цифра». Повышение эффективности производства в данном случае обеспечивается не только за счет автоматического сбора и накопления данных, но и за счет их обработки с помощью инструментов искусственного интеллекта. «Диспетчер» не требует строительства «цифрового предприятия» с нуля. Система представляет собой универсальный готовый шаблон для экстренной цифровизации производства и решения ряда важнейших задач: контроля использования и загрузки оборудования, оценки потерь, оптимизации графиков работы оборудования и персонала, устранения узких мест технологической цепочки, сокращения продолжительности простоев, планирования ТОиР, подключения всего оборудования в единую сеть и многих других.
Система мониторинга «Диспетчер» подключается к любому производственному оборудованию (станкам, обрабатывающим центрам, робототехническим комплексам, контрольно-измерительным машинам, гибким производственным системам) и рабочим местам сотрудников производства с помощью специальных терминалов, регистраторов или обычного сетевого подключения. Данные по локальной сети передаются на сервер, где происходит их обработка и анализ. При этом удается определить нежелательные ситуации, например, простой станков по различным причинам. В этом случае ответственные сотрудники автоматически получают уведомления, после чего принимают оперативные меры по восстановлению рабочей нагрузки. Также «Диспетчер» отслеживает выполнение сменных планов по изготовлению деталей, контролирует и классифицирует причины брака, следит за своевременным выполнением вспомогательных работ, таких как профилактическое обслуживание и ремонт. Сотрудники производства взаимодействуют с системой мониторинга с помощью программного обеспечения АИС «Диспетчер», которое устанавливается на рабочие компьютеры или мобильные устройства персонала. Результаты мониторинга доступны различным службам. Благодаря «Диспетчеру» энергетики предприятия получают подробный анализ по затратам электроэнергии, технологи имеют возможность оптимизировать процессы обработки деталей вплоть до видеонаблюдения за интересующими операциями.
Источник: https://www.intechnology.ru/
Кроме того, «Диспетчер» легко интегрируется с другими IT-системами предприятия, благодаря чему информация о работе оборудования и персонала поступает в различные отделы компании – администрацию, бухгалтерию, ОТК, ОГК и т.д. Система позволяет производить визуальный мониторинг работы оборудования и персонала, настраивать оповещения, генерировать отчеты и анализировать производственный процесс в реальном времени.
Источник: https://www.intechnology.ru/, изображение кликабельно
Результатом внедрения системы мониторинга «Диспетчер» становится увеличение коэффициента использования оборудования, повышение производительности работы станков и, как следствие, увеличение прибыли предприятия. «Диспетчер» позволяет менеджменту компаний существенно повысить эффективность производства и ускорить цифровую трансформацию. Система «Диспетчер» уже установлена на 70 предприятиях по всей России. В среднем она позволяет повысить энегроэффективность на 10%, а эффективность использования оборудования - на 20%.
О компании
Компания «Цифра» (входит в ГК «Ренова») разрабатывает продукты, инвестирует в технологии и развивает среду IIoT и искусственного интеллекта для различных отраслей промышленности. Компания имеет отраслевые продуктовые решения, которые способны повысить эффективность производства в несколько раз. Компания предлагает все элементы для создания «Цифрового предприятия»: системы мониторинга промышленного оборудования и персонала, систему прогнозной аналитики, рекомендательные системы с искусственным интеллектом и платформу промышленного интернета вещей.

Назад