Производство «с умом»: как ИИ и IIoT помогают экономить
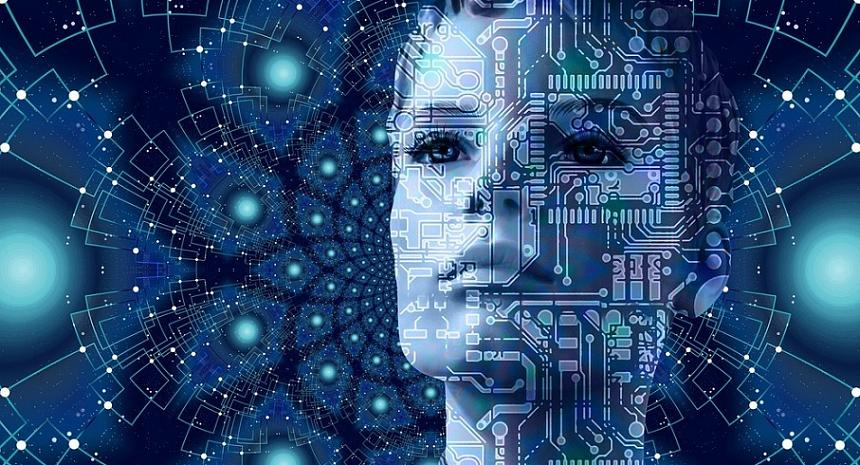
До 90% лишних расходов производства можно избежать, убрав «человеческий» фактор: когда за состоянием оборудования следят датчики, а за качеством продукции – искусственный интеллект (ИИ), эффективность предприятия возрастает многократно.
По прогнозу Минкомсвязи, российский рынок решений в сфере искусственного интеллекта вырастет с 2,1 млрд рублей в 2018 году до 160,1 млрд в 2024 году. ИИ к этому времени займет уже заметную долю в ВВП страны - 0,8%. Но вклад цифровых технологий в экономику будет намного существеннее при активном внедрении решений с использованием искусственного интеллекта в промышленности.
По производительности труда Россия отстает от развитых стран в 2 и более раз. Внедрение современных систем автоматизации производства с использованием технологий промышленного интернета вещей (IIoT) и искусственного интеллекта может в течение первого года увеличить производительность труда на конкретном предприятии в разы. Повсеместное применение подобных решений в отечественной промышленности может дать прирост ВВП страны.
Датчики не обманешь
Технологии IIoT и ИИ уже применяются в рамках системы мониторинга промышленного оборудования. Станки и машины оснащаются датчиками в зависимости от типа производства (датчики температуры, вибрации, давления, расхода воздуха, анализаторы газа и т.п.). Информация с них поступает в систему, которая ее анализирует.
Менеджмент в режиме реального времени получает полное понимание того, что происходит на производстве: о режиме и времени работы оборудования, загрузке каждого станка и его техническом состоянии. Это достоверная информация, а не та, которая занесена вручную и выгодна механикам или инженерам. Например, если агрегат стоит несколько миллионов долларов и простаивает ⅔ времени – можно сделать вывод об эффективности управления производством. А если поступил сигнал о том, что станок работает на запредельных оборотах, принимается решение о необходимости осмотра для предупреждения поломки. Заявку на осмотр система формирует и отправляет сама.
Система мониторинга позволяет изменить принципы технического обслуживания и ремонта оборудования (ТОиР): перейти на режим наладки по состоянию, а не по плану. Объективные данные по работе оборудования позволяют рассчитать точные сроки амортизации, эксплуатации и необходимости обслуживания. Например, на заводе положено устанавливать два насоса: один из них работает, другой в резерве на случай поломки первого. Подходит время техобслуживания. При плановом ремонте их обязаны обслужить в одинаковом объеме. Но объективно в этом нет необходимости: второй насос весь период не работал, достаточно провести минимальные профилактические работы. Система мониторинга позволяет производить ТОиР по реальной необходимости, что существенно экономит затраты предприятия.
Машина зрит в корень
Дальнейшее накопление данных, глубокий анализ и машинное обучение позволяют получать массу прикладной информации. Например, фиксировать подозрительные ситуации, предшествовавшие поломкам или авариям, и в дальнейшем учитывать эти маркеры. Анализируются не только негативные сигналы, но и положительный опыт: где-то добились отличных результатов, можно распространить практику на другие элементы цепочки.
Другой пример: есть несколько однотипных станков с разными комплектующими, которые применялись при ремонте. Собирая статистику, можно обнаружить, что комплектующие от поставщика А более долговечны, а от поставщика Б – требуют замены раньше положенного срока. Значит, на основании объективной информации мы отказываемся от поставщика Б и продолжаем сотрудничать с поставщиком А.
Такая система мониторинга, настроенная в соответствии с отраслевыми стандартами, приносит экономический эффект, в разы превосходящий стоимость внедрения. Развитие технологий ИИ поможет практически исключить человеческий фактор из всего производственного процесса.
Появились решения, позволяющие использовать машинное зрение в системе автоматизации производств. Технология распознавания образов может дополнить систему мониторинга, помогая оценивать техническое состояние оборудования по фото или видео. Кроме этого, она может быть использована для повышения качества продукции. Например, сравнение реального процесса производства (фото или видео) с планограммой (как должно быть) позволяет на раннем этапе выявить брак. В дальнейшем в зависимости от технологического процесса дефект устраняется перед передачей на следующий этап или деталь отсеивается. Так минимизируется потенциальная упущенная прибыль.
Очередь не стоит
У промышленных предприятий появилась возможность получать, обрабатывать, накапливать большие объемы знаний. То, что раньше было сопряжено с выездами, осмотрами, заполнением формуляров вручную, теперь делается моментально в режиме онлайн. Полная, объективная информация и алгоритмы прогнозирования позволяют повысить эффективность производства и прибыльность компании.
Такие системы уже применяются у нас в промышленности: как на крупных оборонных предприятиях, так и гражданских. По нашим оценкам, современные цифровые технологии освоили не более 10% производственных компаний. Проблема - в инертности топ-менеджмента. В крупных компаниях, как правило, нет четкой системы мотивации, когда менеджеры среднего и высшего звена заинтересованы во внедрении новых технологий. К сожалению, управленческий процесс построен так, что им проще ничего не делать. Поэтому для цифрового прорыва в промышленности, в первую очередь, важна инициатива собственников и пересмотр системы мотивации на предприятиях.
Роман Коновалов, президент группы компаний СиДиСи (CDC)

Назад